6/15/2009
Getting Tubed
Chris Beytes
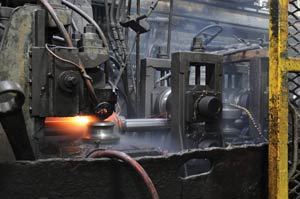
Seventeen thousand acres. That’s how much greenhouse space has been built with steel supplied by Allied Tube & Conduit since the company first entered the greenhouse industry some 20 years ago. And with a new half-million sq. ft. warehouse addition slated to open this winter, Allied looks to be set to provide that much more.
Because it’s Allied’s 50th Anniversary (and because we never miss a chance to wear a hard hat and ear plugs), GrowerTalks recently toured Allied’s Harvey, Illinois, plant with Global Marketing Director Dan Kuzniewski (who also serves as the Communications Committee chairman of the National Greenhouse Manufacturer’s Association) to get a better appreciation for where all that greenhouse steel comes from.
Allied was founded in 1959 by a young engineer named Ted Krengel, who invented a technique for running welded tubing through a zinc bath while it was still on the forming line. Dubbed “Flo-Coat,” the process saved considerable time and handling over existing technologies.
Ted opened his first plant in 1960 with 10 employees and one tube-forming mill. Today, as a division of Tyco Electrical and Metal Products, Allied has plants in Illinois, Arizona, Pennsylvania and Wisconsin, as well as sister operations in Australia, Brazil and the UK. The Harvey plant, Allied’s largest, has 10 mills that each form tubing or other metal profiles 24 hours a day, five days a week. They can also bend, punch, cut and swage steel for their customers, to deliver a more finished part. Allied cranks out a significant amount of tubing on a daily basis, supplying to greenhouse manufacturers as well as 60 other industries. Besides greenhouse structures, the steel goes into a wide range of industrial and structural applications.
We asked Dan if, because of the economy, growers or greenhouse manufacturers are looking for lower-priced steel options. He replied that, despite Allied’s high quality and high technology, their tubing isn’t necessarily more expensive than other options.
“Because we’re a large steel buyer, we obviously have leverage due to the amount of steel that we buy,” he says. “From a company-wide perspective, we convert more than a million tons of steel a year. There are people that sell on price, others that sell on quality, and even others on service. We aren’t one-dimensional, and we can demonstrate sustainability by delivering the whole package.”
So why should a grower want Allied tube in their new greenhouse?
“We truly feel we have the best quality out there, the product that’s going to give you the best service life in the field for your structure,” Dan answered. “It’s certainly a proven and name-recognized product. So you get the feeling that if you’re buying from a manufacturer who’s using an Allied product, you can rest assured that you have a high-quality, well-built structure.”
Dan admits that the economy has put a damper on steel demand—and that includes Allied’s greenhouse business. “In general, we’re not happy with a lot of the markets that we’re in. We do have the financial wherewithal and long-term stability to weather the storm. So [greenhouse] manufacturers and growers will know that we’ll be there to supply them when they’re ready to build again. A lot of smaller mills may have a hard time enduring these times that we’re going through.”
To wrap up, we asked a very technical question: What’s the difference between “conduit,” “pipe” and “tubing”?
Conduit is for carrying wires and serving as a grounding agent in an electrical system. Pipe is based on standard inside diameters and wall thicknesses—such as “Schedule 40”—and is meant for carrying liquid or gas. Tubing is measured by the outside diameter, and there are multiple wall thicknesses available, and it’s used for a wide range of purposes, both structural and mechanical, from greenhouse posts to lawnmower handles.