6/1/2021
Shipping Woes
Jennifer Polanz
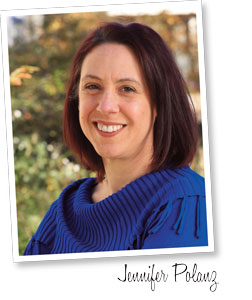
In working on the story about garden décor this month, I received an education in the current state of shipping, which, in a few words, is not great right now. It’s not only a fascinating story, but it impacts everyone and it behooves us all to understand why we’re seeing shortages, delays and increased costs.
It all starts overseas at a multitude of factories in Asia—everywhere from China to Vietnam, Thailand, Indonesia and other countries that have manufacturers churning out all manner of products. The shipping process is a bit like the choreography of a busy highway—smooth-flowing and fast(ish) when it’s working, and bottlenecked like a highway under construction with closed lanes when it’s not working. Right now, we’re looking at one lane open and backed up for miles.
Why? The person in the garden décor world who detailed this for me emphasized a key fact that helps to understand the tight logistics of shipping: when a factory produces enough product to fill a container for a company, a broker has to book the container and the spot on the cargo ship, and they have to get the product on the container and loaded onto the ship within just a few days. That prevents product from taking up containers while sitting waiting for spots on cargo ships. That’s a tight turnaround in good times.
Now, add COVID-19 to the mix. Late last winter, some factories shut down and sent workers home, while others introduced COVID protocols and kept producing (depending on the country). The ships that were already on the seas went to their destination port, and those containers were unloaded and delivered to the importer. Then the containers were transported back to the port and sat empty. The ships that would normally bring the empty containers back to Asia quit sailing so containers wouldn’t pile up at ports there. When the wheels of production began to slowly turn again, those empty containers came back to Asia at a snail’s pace, creating a huge demand (remember, some factories never shut down and had product ready to ship). That demand resulted in shipping costs doubling in some cases, which explains increases you may be seeing on your bill of lading.
It also explains why you may experience delays in receiving product or only receive partial shipments. The factories shipped what they’d made, but that may only have been part of what you ordered, and the rest was made later (or is yet to be made) and is waiting for another container and ship to become available.
There are other opportunities for bottlenecks, too. Massive container ships often stop at ports close to the U.S. East Coast and offload containers to smaller ships that then fan out across the Eastern seaboard to deliver product. They can often get delayed during that transfer process, making it more of a days- or weeks-long layover versus a quick pit stop.
It’s certainly not just garden décor that’s affected, either. We’ve heard of issues ranging from bags for bagged goods to spray nozzles and bottle caps for products and even plastic pot shortages. Everyone I talked to thought it would take about five to six more months for shipping to normalize.
I know this doesn’t help when customers are clamoring for product, but it’s one of those “we’re-all-in-this-together” sort of moments. But, hey, at least now we have a steady supply of toilet paper. GP